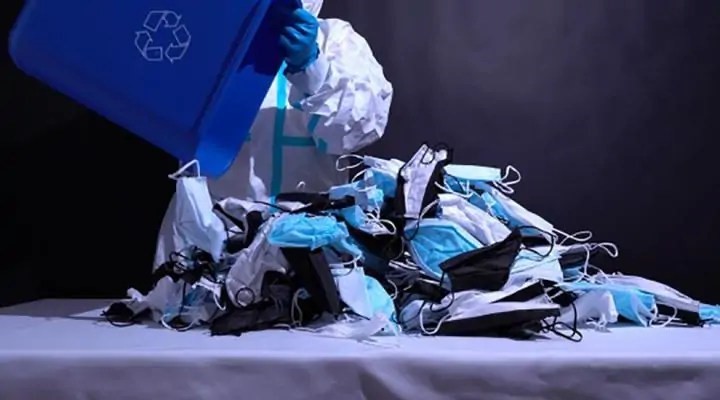
Turning waste PPE into water and vinegar
A process to convert PPE waste into harmless by-products is a potential gamechanger to the problem of PPE waste filling landfills and polluting oceans and rivers.
Shredded masks, gowns, gloves and plastic safety glasses go into a machine; hot, pressurized water and compressed air are applied; water and acetic acid are the end-products. The PPE-to-liquid process is carried out at a temperature of 300°C and takes about an hour in a small prototype machine in a laboratory in the faculty.
Gaseous by-products from the process are Oxygen and low concentrations of Carbon dioxide which can be safely discharged. "This is a clean, chemical-free solution which will be a game changer internationally.
The technology used is a hydrothermal deconstruction or valorisation process and it destroys the waste completely. The liquid produced in the process is safe, inert and can be reused—the vinegar or acetic acid can be used for disinfecting and the water can be reused for the processing cycle therefore minimizing water consumption and helping with sustainability.
By developing two technologies—one for reusable waste and the other for waste that cannot be reused or recycled—we are closing the loop on this ever-growing serious waste issue and providing a circular solution that truly is clean and green.
The research teams are now taking steps to develop the solutions into a larger scale pilot system and, learning from that, will develop a full-scale proof-of-concept.